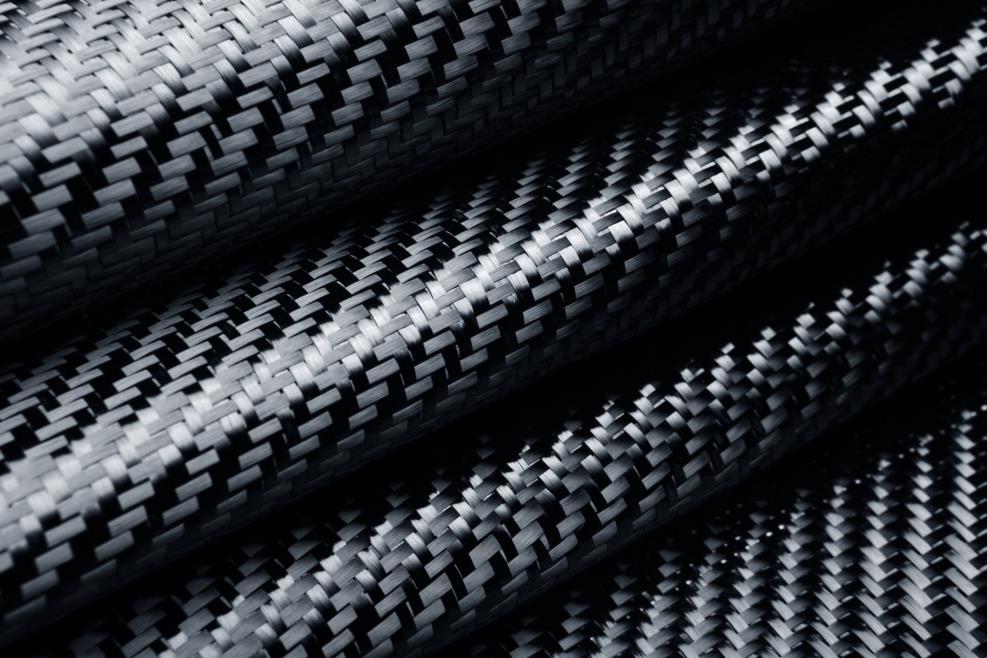
1. Carbon Fibre (CF)
Composition
Carbon fibres are made from precursor materials (such as polyacrylonitrile or pitch) that are heated and carbonised.
Properties
- Exceptionally high tensile strength: CF can withstand significant loads without breaking.
- Low density: lightweight, contributing to fuel efficiency.
- High stiffness: Provides structural integrity.
- Excellent fatigue resistance is vital for long-term durability.
Applications
- Primary Structures: Wings, fuselage, tail sections, and landing gear components.
- Interior Components: Seats, overhead bins, and floor panels.
Challenges
- Cost: Production of carbon fibre composites is expensive.
- Impact Sensitivity: susceptible to damage from impacts.
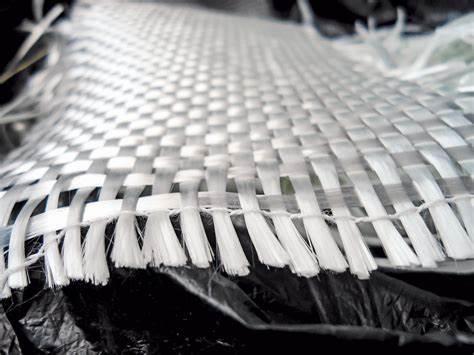
2. Glass Fibre (GF)
Composition
Glass fibres are made from molten glass that is drawn into thin strands.
Properties
- Moderate tensile strength: adequate for non-structural parts.
- Lower stiffness compared to carbon fibres.
- Good electrical insulation properties.
Applications
- Fairings: exterior coverings for streamlined aerodynamics.
- Interior Panels: Cabin walls, ceilings, and partitions.
- Secondary Structures: non-critical components.
Limitations
Moisture Absorption: Glass fibres can absorb water over time. Aramid fibre.
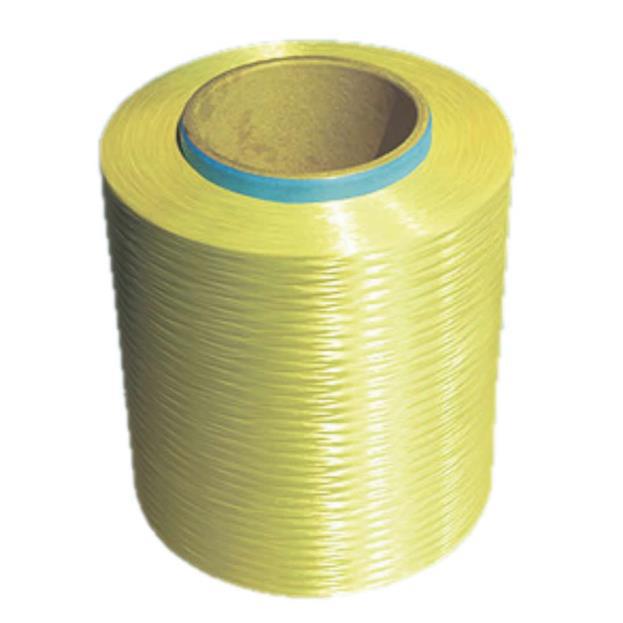
3. Aramid Fibre (AF) (e.g., Kevlar)
Composition
Aramid fibres are synthetic polymers with repeating aromatic units.
Properties
- High impact resistance: used in protective applications.
- Excellent strength-to-weight ratio.
- Lightweight.
Applications
- Protective panels: bulletproof vests, cockpit doors.
- Aircraft armour: critical areas requiring impact resistance.
Drawbacks
Lower Stiffness: Not as rigid as carbon fibres.
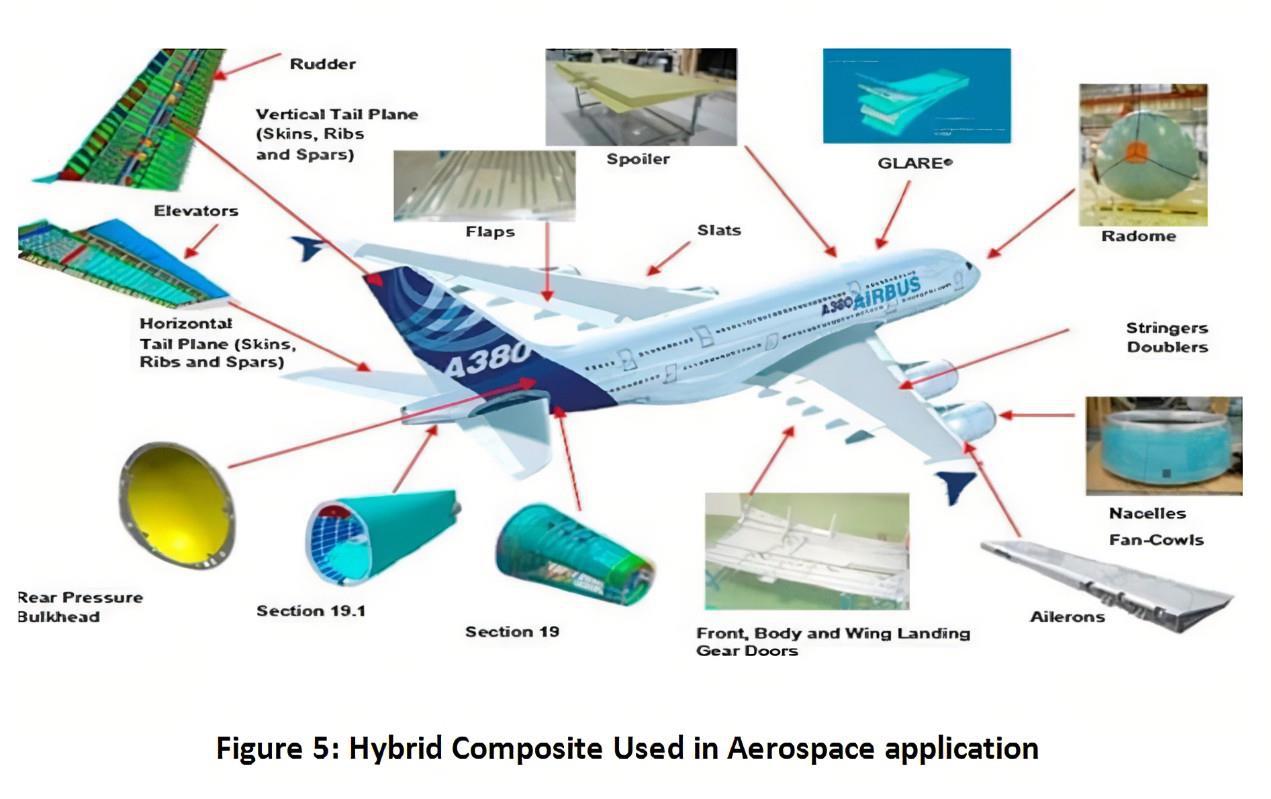
4. Hybrid Composites
- Combine different fibre types (e.g., carbon and glass) to optimise properties.
- The product is tailored for specific requirements (e.g., stiffness in one direction, toughness in another).